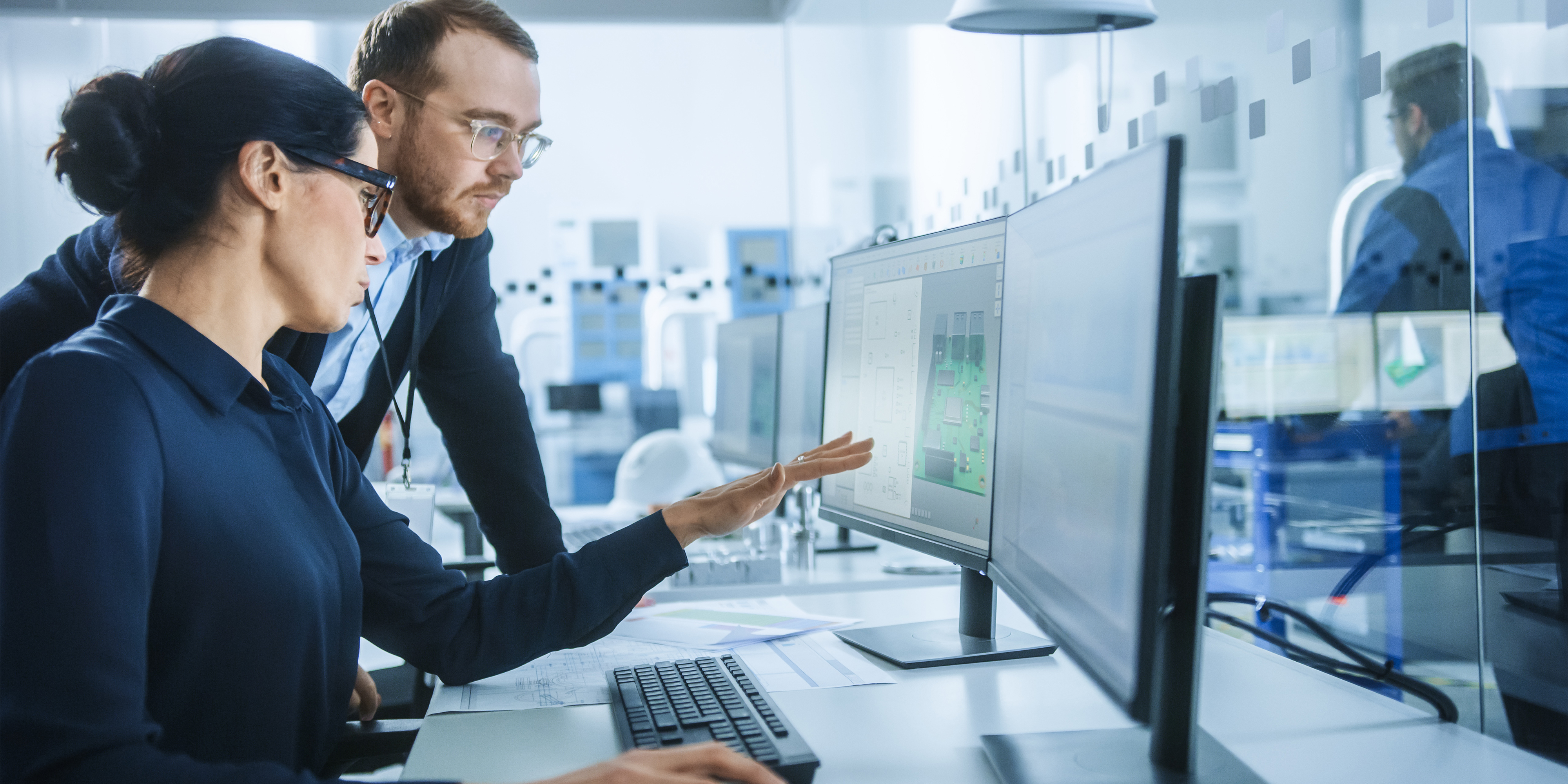
Progettare una scheda custom: in cosa consiste e quando conviene
Scritto il . Pubblicato in Elettronica custom,progettazione.
A chi conviene fare progettare una scheda elettronica custom, e quali sono i costi che questo processo implica?
Spesso i costi di progettazione vengono vissuti dall’imprenditore come uno scoglio iniziale per valutare se iniziare a produrre un nuovo macchinario. Vediamo come e quando conviene affrontare il progetto per lo sviluppo di un hardware custom.
Quando è vantaggioso far progettare una scheda elettronica custom?
Questa operazione conviene all’imprenditore o al direttore tecnico di un’azienda che produce macchinari in serie, tutti identici tra loro.
Un progetto di elettronica custom è dedicato allo sviluppo di un nuovo macchinario; deve pertanto introdurre nuove funzionalità o nuove tecnologie. Spesso le funzioni richieste per la scheda sono molto innovative e non esistono sul mercato soluzioni adatte allo scopo. Inoltre, limitatamente alle funzioni che devono essere specifiche per la macchina, la scheda elettronica deve avere costi limitati.
Nel caso in cui nel mercato le soluzioni commerciali presentino costi più alti e non abbiano il tipo di personalizzazione richiesto, allora conviene intraprendere un processo di progettazione di una scheda elettronica custom.
Perché affrontare i costi di progettazione e quale è il reale guadagno?
Di fronte a questa esigenza l’imprenditore si rivolge solitamente a un’azienda di elettronica per un preventivo riguardante un progetto di scheda elettronica custom e la sua produzione.
Vediamo insieme come viene portata avanti una valutazione dei costi.
La prima fase da affrontare è quella di analisi: si impostano, come in un elenco, gli elementi necessari per la scheda elettronica in base alla funzionalità richieste e ai componenti che deve comandare la macchina.
Una volta chiariti i prerequisiti tecnici, si imposta un progetto durante il quale si scelgono i componenti che faranno parte dell’hardware e si compie un’analisi dei tempi e dei costi.
I costi si dividono in:
Costi di progettazione hardware. Spese di impianto e prototipazione solitamente sono incluse in questa voce. Sono costi una tantum, che vengono valutati in base alla complessità del progetto (si tratta di poche migliaia di euro).
- Costi di progettazione firmware, che variano molto a seconda della complessità della scheda e delle funzionalità che devono essere coperte. Ad esempio, per una scheda I/O i costi di sviluppo sono minimi, mentre per una scheda con sistema operativo e gestione di un’interfaccia utente complessa i costi possono anche arrivare a decine di migliaia di euro.
- Listino hardware della scheda, che in base alle quantità diminuirà (più schede vengono prodotte, meno costa la singola scheda).
Se il progetto viene accettato ed approvato, la seconda fase è quella in cui inizia il lavoro dei progettisti hardware e software. Questa fase prevede diverse sotto-fasi, tutte comprese nei costi relativi ai punti 1 e 2 elencati sopra:
Sbroglio HW
-
- prototipazione
- raccolta specifiche firmware e sviluppo
- prototipo funzionante
- test EMC e altri test
- pre-serie e inizio produzione
La terza ed ultima fase è quella della produzione. Per realizzare le schede sono tanti i componenti che devono essere acquistati, e altrettante le operazioni che devono essere messe in atto per arrivare a un prodotto finito funzionante:
- acquisto circuiti stampati,
- acquisto componenti attivi e passivi da montare sulla scheda, compresi microprocessori e moduli vari,
- montaggio,
- collaudo, che si differenzia in base al tipo di collaudo (funzionale, burn-in, in circuit cc),
- assemblaggio (ad esempio se una scheda deve essere posizionata in una scatola ecc.).
Un esempio pratico
Ecco un esempio per capire quando e perché conviene produrre una scheda elettronica custom e dove c’è un reale risparmio sui costi.
Il titolare dell’azienda sente la necessità di fornire un servizio aggiunto al proprio prodotto, un macchinario industriale che viene movimentato all’interno di ambienti chiusi. Ha già un’elettronica di controllo per il comando di tutti i componenti della macchina, ma il servizio viene richiesto anche da alcuni grandi clienti e l’imprenditore non ha intenzione di perdere opportunità commerciali.
L’idea inziale è di raccogliere i dati di produzione della macchina e monitorarli su di un portale web ad uso dell’assistenza tecnica, in modo da poter sapere prima di recarsi dal cliente quali componenti portare per la riparazione e risparmiare tempo. Inoltre, i clienti chiedono di sapere quando e per quanto tempo la macchina è stata in funzione.
Sulla scheda elettronica quindi servono:
- un modulo cellular con SIM card e antenna
- un accelerometro per la rilevazione degli urti
- alcuni ingressi e uscite
- la porta seriale di comunicazione con le altre schede di controllo della macchina
- alcuni ingressi e uscite per sensori
- un modulo RFID per riconoscimento
- un pacco di batterie per far funzionare la scheda anche in caso di macchina spenta
- un modulo Wi-Fi per collegarsi a un app ad uso dell’assistenza tecnica.
Tutto questo, in una soluzione di 11x8 cm a causa del poco spazio disponibile.
I tentativi di realizzare questo progetto con dei componenti commerciali sono stati abbandonati fin da subito.
Il progetto di un nuovo hardware invece, che ha messo insieme tutte queste tecnologie ed ha reso possibile ottenere tutti i benefici richiesti, è costato poche migliaia di euro. Il progetto software ha portato alla realizzazione di un sistema di IoT che dal 2015 a oggi è in continua evoluzione, e ha portato il produttore ad avere un vantaggio competitivo sul mercato rispetto alla concorrenza, che ancora oggi lo sta inseguendo.
Hai un progetto e vuoi parlarne con noi? Contattaci!